A recent Deloitte survey showed that as many as 76% of manufacturers are using digital tools for enhanced supply chain transparency.
With industries facing so many ongoing supply chain challenges, organisations are seeking to improve resilience by investing more in digitisation initiatives that deliver better visibility across the value chain.
One company facilitating this digitisation journey is Appian, a software enterprise that automates business processes. The Appian AI Process Platform includes everything an organisation needs to design, automate, and optimise complex processes, from end to end.
“Appian’s platform enables organisations to digitise their supply chain and achieve their business objectives,” says Gary Cassell, Global Manufacturing & Automotive Industry Lead at Appian.
In his role, Cassell is responsible for the go-to-market planning and execution for its manufacturing and supply chain practice worldwide.
“This means working with Appian team members, system integrators, software partners and customers to ensure Appian's value proposition and technology are understood, applied, and continuously evolving,” he says.
For manufacturing and supply chain, Appian offers a complete enterprise automation platform that links data, technology and business needs.
Unified data crucial for digital transformation
Cassell is perfectly placed to advise customers on the power of unified data. Prior to joining Appian, he had many years of first-hand experience with the problems and limitations posed by siloed data.
“When I was leading businesses and supply chain transformation efforts, siloed data and siloed functional processes were a huge challenge,” he says.
He adds: ”This approach resulted in complex processes, with much of the work happening outside of the source systems, which made it difficult to access data and resulted in poor visibility of issues.”
Cassell says that, depressingly, because of this problem “it was also inevitable that we were going to face the same issues again in the future”.
One of Appian’s USPs is that it unifies data, but without requiring the migration of source-system data, thus removing one of the most challenging aspects of any digital transformation project.
Again, this is a problem of which Cassell has long experience.
He says: “As a lean manufacturing practitioner I believe the best way to solve problems is to make them visible, and also to make data-driven decisions.
“The approach I drove when leading supply chain transformation efforts was to move to a platform, connecting siloed data spread across enterprise systems. Doing so makes the data visible, so the organisation can become more proactive in its decision making.”
Cassell adds that all the platforms he and his past teams studied required the migration of source system data into the platform, and that this part of the transformation actually took the longest.
“While it did produce value, the data-loads were large and delayed load-times limited the value that could be achieved,” he recalls.
Cassell adds: “Unfortunately, we did not know about Appian and the power of data fabric technology, which is just one capability of the Appian Platform,” Cassell says. “The ability to leave data in the source systems and connect to it in the platform would have given us exactly what we needed to have a connected supply chain across the enterprise.”
Appian automates & streamlines end-to-end processes
In addition to this powerful functionality, Appian also automates and streamlines end-to-end processes and delivers ‘private AI’, which protects an organisation’s most important data assets.
It differs from other supply chain solutions in that it provides a single platform for end-to-end process automation. By being a single, unified platform, Appian allows organisations to:
- Rapidly design new digital solutions using low-code design
- Automate workflows with a full set of automation tools, including AI, RPA, and other digital work factors
- Optimise business operations by having visibility around processes.
Cassell says: “Appian has been a pioneer in the realm of AI process automation since as early as 2007, and we are the only platform that brings together data fabric – which unifies data without migration – automation, which streamlines end-to-end processes, and ‘private AI’, which protects your most important data assets.”
Today, Appian’s customers face exacting challenges in both the manufacturing industry and also in supply chain management.
“At a macro level, manufacturers are dealing with inflation, which is impacting margins due to higher material costs,” says Cassell. “Hiring and retaining the labour needed to meet demand is another issue, as is dealing with widening skill gaps and higher wages.”
He adds that there are also ongoing challenges with supply chain constraints, which are impacting not only costs, but also customer service levels, and says such problems mean it’s imperative manufacturers adopt strategies to stay agile enough to continue delivering, despite supply chain issues.
Manufacturers striving for agility in a tough market
To achieve the required agility, many manufacturers are diversifying their supplier base and shortening their supply chain for critical components.
“Manufacturers can identify and partner with multiple suppliers to reduce dependence on a single source and onshore or near shore suppliers to shorten their supply chain,” says Cassell. “This helps mitigate supply chain disruptions caused by factors such as natural disasters, geopolitical risks, or other unforeseen events.”
There is also predictive analytics, whereby manufacturers leverage data analytics to forecast demand and identify potential supply chain bottlenecks. This helps them proactively plan, and adjust production schedules to ensure timely delivery.
Collaborative partnerships are also important, says Cassell.
“Manufacturers can collaborate with suppliers, customers, and other stakeholders to identify potential supply chain risks and develop contingency plans,” he says. “This can help build resilience and improve supply chain visibility.”
In the quest for agility, many organisations are also opting to use a platform approach, to ensure their supply chain and production systems are flexible and agile, which of course is where Appian comes in.
Appian’s platform is important because it enables organisations to:
- Unify siloed data in real time, instead of forcing another expensive redundant data-store
- Enable the end-to-end hyper-automation of processes
- Connect internal and external stakeholders
- Mine processes to discover issues to eliminate bottlenecks
- Provide employees with 360-degree views of the information they need without having to go to multiple source systems
Cassell says that in order to move towards a connected supply chain, organisations must leverage technologies that digitise and automate end-to-end supply chain processes “in order to connect both the organisation internally and also to connect customers and partners”.
Examples of such disruptive technologies include:
- An enterprise scalable platform, which extends source systems and enables collaboration and secure information flow between all involved parties in the supply chain
- Process mining, to accelerate discovery of the current real process as well as where bottlenecks are occurring
- Workflow and case management, to ensure all parties are connected and communicating to drive the best overall outcomes.
- A full automation platform that enables automated processes using technologies like Cloud, RPA, IoT and AI/ML to enable connectivity and transparency to make supply chains more alert and composable
- Data fabric technology, to give real-time visibility and execution, versus the need to migrate data into another tool leading to delays and reconciliations of redundant data sources
- A low-code platform that offers tools to digitise and automate supply chain processes and accelerate time-to-value
Cassell says that, from a technology standpoint, having the ability to create a supply network that collaborates, shares information, and is transparent is imperative “because a connected supply chain enables organisations to be more agile, responsive and competitive in today’s complex business environment ”.
He adds: “There are technologies that will enable organisations to overcome the current challenges of data silos and the disconnected network. It’s not a case of ‘Do it today and it’s complete tomorrow’, but investing in the right platform to enable the journey, by investing in technology that can evolve with the ever-changing business environment.”
Everything always comes back to the data
Regardless of the technologies involved, everything always comes back to the data needed to deliver real-time and end-to-end process visibility. It is unified data, Cassell points out, that helps make supply chain planning a proactive rather than reactive discipline.
Appian helps with supply chain planning by providing better visibility, predictive alerts to mitigate disruptions and by facilitating broader collaboration with suppliers.
“Appian’s advanced case-management capabilities provide a unique capability to elevate an organisation's integrated business planning process,” explains Cassell.
He adds that by orchestrating multiple stakeholders, Appian brings both efficiency and visibility to the process, and does so by connecting an organisation's most valuable asset – its people – to the process, “to ensure the best overall result”.
Appian, says Cassell, also integrates “the execution layer” into the planning process, which allows manufacturers to “sense and predict risks as well as changes in demand patterns”. These, he adds, “can be integrated into the planning process in real-time to enable an agile planning process”.
It is not just in the area of supply chain planning that Appian is used; it is deployed in many other areas.
“Customers use it across all the functional areas – planning, sourcing, manufacturing, delivering, returning,” says Cassell, who adds: “For example, at the platform level, Appian can identify an order at risk and then alert the order-management team. It can also make recommendations on how to solve that issue and orchestrate the solution, which might be to direct shipping from another location or supplier. This is a lot of manual work for order management representatives in most organisations.”
Customers also use Appian to automate manual or paper-driven processes, whether in the supply chain or production processes, and another major task it can handle includes orchestrating new-product introduction processes, to bring products to market faster.
“The Appian platform can provide an end-to-end digital thread of a product, versus a partial digital thread, which is more common,” Cassell explains.
Appian’s broad-based and potent functionality is the result of 25 years spent understanding, changing, testing, and constantly improving enterprise processes.
“Appian is built for the complexity, scalability, and security that mission-critical apps require,” Cassell says, and adds: “In addition to our leading data fabric technology, process automation expertise and dedication to private AI-powered experiences, we also deliver a superior user experience across desktop and mobile devices.”
Make sure you check out the latest edition of Supply Chain Digital Magazine and also sign up to our global conference series - Procurement & Supply Chain LIVE 2024
**************
Supply Chain Digital is a BizClik brand
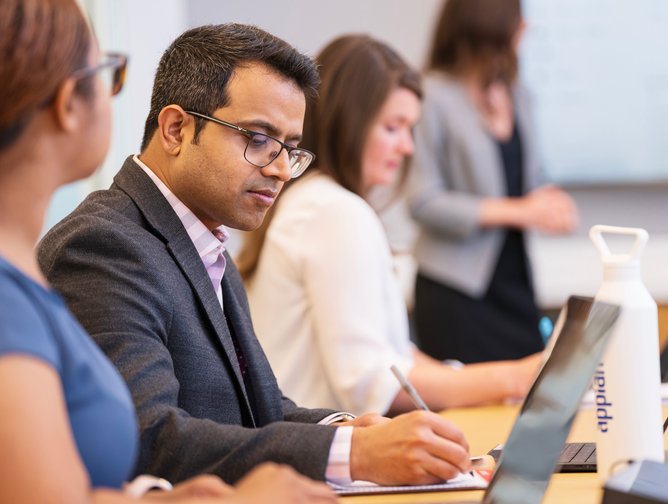
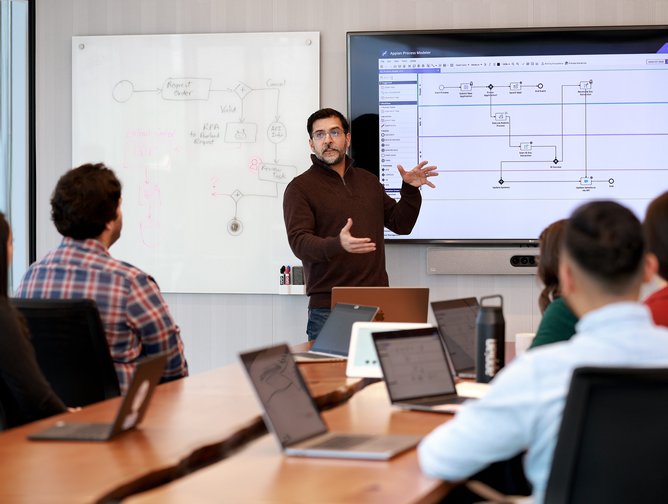
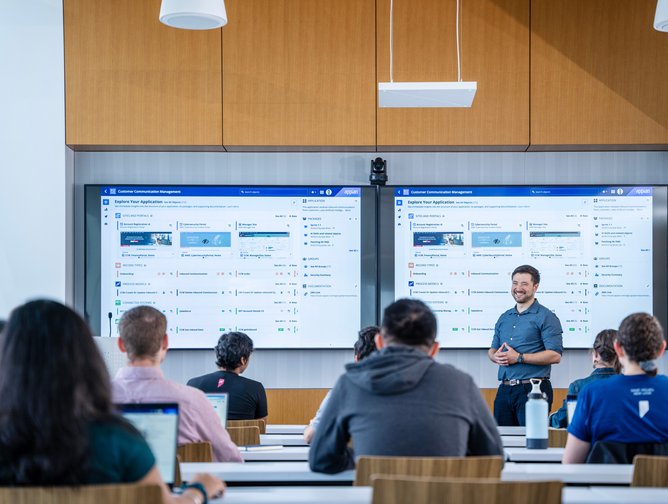
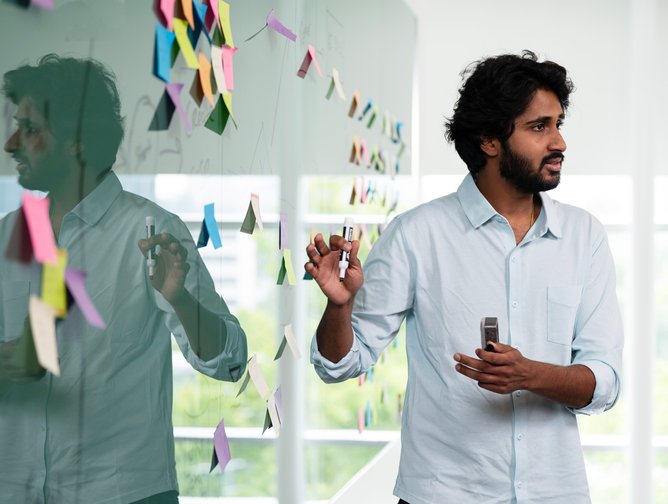